Instalacja CO w Układzie Zamkniętym: Schemat i Kluczowe Elementy 2025
W obliczu rosnących wymagań stawianych nowoczesnym systemom grzewczym, wybór odpowiedniego rozwiązania bywa prawdziwym dylematem. Czy myślimy o tradycyjnym cieple, czy futurystycznej efektywności, centralnym punktem jest zawsze to, jak ciepło dotrze do naszych grzejników. Jednym z kluczowych pojęć, które napotkamy podczas planowania lub modernizacji, jest schemat instalacji co w układzie zamkniętym. Czym właściwie jest ten intrygujący układ i dlaczego budzi tyle zainteresowania? Najprościej mówiąc, to bezpieczny, nadciśnieniowy system grzewczy, który w odróżnieniu od swoich starszych, otwartych odpowiedników, działa pod stałym ciśnieniem, wykorzystując zamknięte naczynie wzbiorcze i minimalizując kontakt czynnika grzewczego z powietrzem.
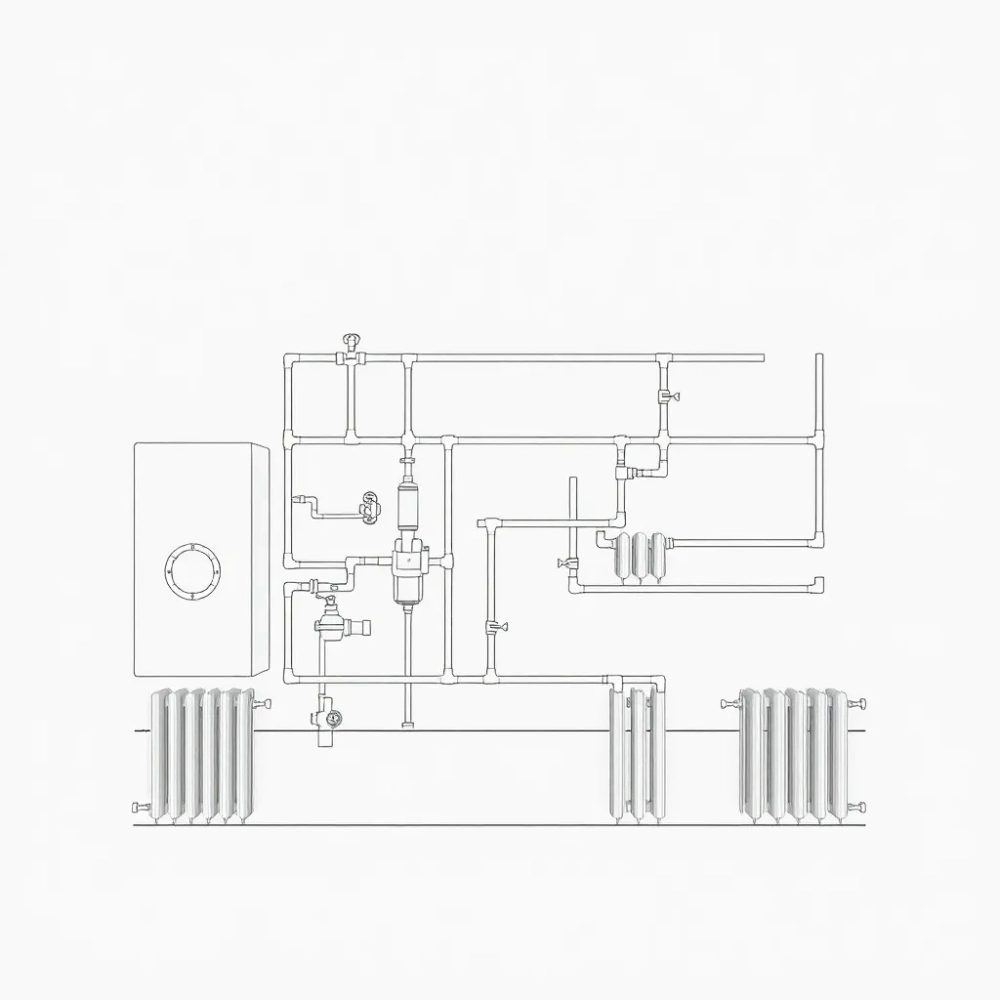
Analizując dostępne dane i obserwacje rynkowe dotyczące instalacji centralnego ogrzewania, można zauważyć wyraźne tendencje preferencji użytkowników i instalatorów w zależności od kluczowych parametrów systemów grzewczych.
Cecha / Charakterystyka | Układ Otwarty (Szacunkowo / Typowo) | Układ Zamknięty (Szacunkowo / Typowo) | Komentarz |
---|---|---|---|
Typ Naczynia Wzbiorczego | Otwarte (do atmosfery) | Membranowe (zamknięte, ciśnieniowe) | Kluczowa różnica konstrukcyjna i zasada działania. |
Ciśnienie Robocze (Typowe) | Statyczne (np. 0.1 - 0.5 bar powyżej atmosferycznego) | Robocze (np. 1.5 - 2.5 bar) | Układ zamknięty pracuje pod wyższym, kontrolowanym ciśnieniem. |
Kontakt Czynnika Grzewczego z Powietrzem | Bezpośredni | Brak lub minimalny | Ma wpływ na korozję i wymagania dotyczące jakości wody. |
Ryzyko Korozji Wewnętrznej | Wyższe (dostęp tlenu) | Niższe (brak tlenu) | Tlen jest głównym czynnikiem przyspieszającym korozję w instalacji. |
Ryzyko Zamrożenia Naczynia | Tak (jeśli umieszczone np. na nieocieplonym strychu) | Nie | Membranowe naczynie można instalować w kotłowni. |
Maksymalna Temperatura Pracy (praktyczna) | Ograniczona do 100°C (temperatura wrzenia pod ciśnieniem atm.) | Wyższa (>100°C możliwe dla odpowiednich komponentów, standardowo 80-90°C) | Pozwala na pracę z kotłami wymagającymi wyższych temperatur. |
Konieczność Uzupełniania Wody | Częste (parowanie z naczynia) | Sporadyczne (drobne wycieki) | Wpływa na koszty eksploatacji i serwisowania. |
Wymagania dotyczące Rurociągów (obiegu grawitacyjnego) | Duże średnice, specyficzne spadki | Mniejsze średnice możliwe, dowolne prowadzenie (obieg wymuszony) | Duża swoboda projektowania instalacji zamkniętych. |
Orientacyjny Koszt Naczynia Wzbiorczego (przykład: dom 150m²) | Proste, otwarte - np. 100-300 PLN | Membranowe - np. 300-600 PLN (typowo 25-50 litrów) | Różnica w cenie samych komponentów jest zauważalna, ale system to całość. |
Przedstawione zestawienie cech wyraźnie wskazuje, że wybór systemu CO to coś więcej niż tylko preferencja estetyczna czy kaprys. Widać jak na dłoni, że układ zamknięty, choć potencjalnie nieco droższy w zakupie samego naczynia wzbiorczego, oferuje znaczące korzyści długoterminowe. Niższe ryzyko korozji przekłada się na dłuższą żywotność całego systemu grzewczego, a wyższa elastyczność projektowa ułatwia instalację w nowoczesnych budynkach, gdzie estetyka i optymalizacja przestrzeni są kluczowe. Co więcej, fakt pracy pod ciśnieniem pozwala na precyzyjniejszą kontrolę nad temperaturą i przepływem czynnika grzewczego, co w konsekwencji może prowadzić do większej efektywności energetycznej.
Zatem, choć początkowy schemat instalacji CO w układzie zamkniętym może wydawać się bardziej skomplikowany na pierwszy rzut oka z powodu konieczności zastosowania bardziej zaawansowanych zabezpieczeń, jak zawory bezpieczeństwa czy urządzenia do odbioru nadmiaru ciepła, to właśnie te elementy budują jego przewagę nad tradycyjnymi rozwiązaniami otwartymi, zapewniając spokój ducha i bezproblemową eksploatację przez lata.
Kluczowe Elementy Składowe Schematu Instalacji CO w Układzie Zamkniętym
Gdybyśmy mieli wskazać serce systemu centralnego ogrzewania w układzie zamkniętym, byłby nim z pewnością kocioł grzewczy. Jednak w kontekście różnic konstrukcyjnych i fundamentalnych dla charakterystyki układu, absolutnie kluczowym elementem, który odróżnia go od układu otwartego, jest zastosowanie zamkniętego, membranowego zbiornika ciśnieniowego, zwanego potocznie naczyniem wzbiorczym membranowym.
W odróżnieniu od otwartego naczynia, które komunikuje się swobodnie z atmosferą, membranowy zbiornik ciśnieniowy to hermetycznie zamknięta stalowa puszka, podzielona wewnątrz elastyczną membraną gumową na dwie komory: jedną dla wody instalacyjnej i drugą wypełnioną gazem (zwykle azotem lub sprężonym powietrzem) pod odpowiednim ciśnieniem wstępnym.
Jego rola jest nie do przecenienia – przyjmuje on zwiększającą objętość wodę instalacyjną w miarę wzrostu temperatury czynnika grzewczego. Gdy woda w systemie się nagrzewa, rozszerza się, zwiększając ciśnienie. Zamiast wylewać się, jak w układzie otwartym, woda ta jest wpychana do komory wodnej naczynia wzbiorczego, ściskając gaz w komorze gazowej. Dzięki temu ciśnienie w systemie wzrasta w sposób kontrolowany, ale nie osiąga krytycznych wartości, które mogłyby uszkodzić rury czy inne komponenty.
Kiedy system stygnie, a woda kurczy się, ciśnienie wstępne gazu w naczyniu wypycha wodę z powrotem do instalacji, zapobiegając spadkowi ciśnienia poniżej akceptowalnego minimum i potencjalnemu zapowietrzaniu się systemu. Odpowiedni dobór rozmiaru naczynia jest absolutnie fundamentalny dla poprawnego działania i bezpieczeństwa systemu. Zbyt małe naczynie nie pomieści rozszerzającej się wody, powodując częste otwieranie zaworu bezpieczeństwa i utratę wody z systemu. Zbyt duże, choć bezpieczne, stanowi niepotrzebny koszt i zajmuje więcej miejsca.
Generalna zasada doboru mówi, że objętość naczynia wzbiorczego powinna wynosić minimum 6-8% całkowitej objętości wody w instalacji, ale dokładny dobór zależy od wielu czynników: całkowitej objętości instalacji, maksymalnej i minimalnej temperatury pracy, a także ciśnienia wstępnego gazu i maksymalnego ciśnienia roboczego. Dla typowego domu jednorodzinnego o powierzchni 150-200 m² z instalacją grzejnikową, orientacyjna objętość wody może wynosić od 150 do 300 litrów. W takim przypadku potrzebne będzie naczynie wzbiorcze o pojemności co najmniej 12 do 25 litrów, ale dla zachowania zapasu bezpieczeństwa często instaluje się naczynia 25-litrowe, 35-litrowe, a nawet 50-litrowe, zwłaszcza przy większej liczbie grzejników czy podłogówce (która ma zazwyczaj większą objętość wody). Cena takich naczyń waha się zazwyczaj od 300 do 800 PLN w zależności od pojemności i producenta.
Instalacja naczynia wzbiorczego membranowego powinna odbywać się na rurociągu powrotnym, jak najbliżej króćca ssawnego pompy obiegowej (lub samego kotła, jeśli pompa jest wbudowana). Zapewnia to najbardziej stabilne warunki pracy hydraulicznej dla naczynia.
Oprócz naczynia wzbiorczego, zamknięty schemat instalacji grzewczej wymaga obecności innych, kluczowych elementów. Jednym z nich jest manometr – ciśnieniomierz, montowany w łatwo dostępnym miejscu instalacji (zwykle na kotle lub w jego pobliżu). Pozwala on na bieżące monitorowanie ciśnienia w systemie. Typowe ciśnienie minimalne (na zimno, przy ok. 20°C) powinno wynosić np. 1.2-1.5 bara dla domu parterowego, lub odpowiednio wyższe, by zapewnić ciśnienie ok. 0.5-1.0 bara na najwyższym punkcie instalacji. Ciśnienie maksymalne robocze nie powinno przekraczać np. 2.5 bara, a ciśnienie zadziałania zaworu bezpieczeństwa to najczęściej 3 bary.
Fundamentalnym dla bezpieczeństwa elementem jest również zawór bezpieczeństwa – termiczny lub ciśnieniowy. W układzie zamkniętym jest on absolutnie obowiązkowy i jego prawidłowe działanie jest kwestią życia lub śmierci (dosłownie w przypadku awarii). Zawór bezpieczeństwa ciśnieniowy otwiera się samoczynnie, gdy ciśnienie w instalacji przekroczy określoną, bezpieczną wartość (np. 3 bary dla większości instalacji domowych), upuszczając nadmiar wody do kanalizacji. Chroni w ten sposób instalację przed rozsadzeniem na skutek nadmiernego wzrostu ciśnienia spowodowanego przegrzaniem lub awarią naczynia wzbiorczego. Montowany jest zazwyczaj bezpośrednio na kotle lub w jego najbliższym sąsiedztwie, zawsze na nieuzbrojonym odcinku rury, tj. bez żadnych zaworów odcinających pomiędzy kotłem a zaworem bezpieczeństwa. Cena standardowego zaworu bezpieczeństwa 3 bar z gwintem G½” to zazwyczaj od 30 do 80 PLN.
W przypadku kotłów na paliwo stałe w układzie zamkniętym (o czym szerzej w kolejnych sekcjach), konieczne są dodatkowe zabezpieczenia termiczne, ale sam schemat bazowy dla większości kotłów (gazowych, olejowych, elektrycznych) w układzie zamkniętym opiera się o te trzy filary: kocioł, naczynie wzbiorcze membranowe i zawór bezpieczeństwa ciśnieniowy.
Pamiętajmy, że każdy element ma swoją specyfikę i wymaga odpowiedniego doboru oraz montażu zgodnego z instrukcją producenta i obowiązującymi normami. Bagatelizowanie roli któregokolwiek z tych komponentów jest igraniem z ogniem. Dobrze zaprojektowany i wykonany schemat techniczny instalacji CO w układzie zamkniętym to gwarancja bezpieczeństwa i komfortu użytkowania na długie lata.
Kolejne ważne części składowe to armatura regulacyjna i odcinająca – zawory, filtry (osadniki), odpowietrzniki. Zawory odcinające umożliwiają odłączenie poszczególnych sekcji instalacji (np. grzejnika) bez konieczności opróżniania całego systemu, co jest ogromną zaletą podczas prac serwisowych czy wymiany. Filtry chronią pompę obiegową i kocioł przed zanieczyszczeniami krążącymi w wodzie instalacyjnej. Odpowietrzniki (ręczne lub automatyczne) służą do usuwania powietrza z instalacji, które może powodować hałas, utrudniać cyrkulację i prowadzić do korozji.
Nieodzownym elementem układu wymuszonego (standard w układzie zamkniętym) jest pompa obiegowa. To ona zapewnia prawidłowy przepływ czynnika grzewczego od kotła do odbiorników ciepła (grzejników, pętli ogrzewania podłogowego) i z powrotem. W zależności od wielkości instalacji i zapotrzebowania na moc, stosuje się pompy o różnej wydajności. Nowoczesne pompy elektroniczne (energooszczędne) automatycznie dostosowują swoją pracę do aktualnych potrzeb systemu, co przekłada się na niższe zużycie energii elektrycznej. Koszt pompy obiegowej do domu jednorodzinnego to zazwyczaj od 300 do 800 PLN za model elektroniczny.
Podsumowując ten rozdział, schemat kompletnej instalacji CO w układzie zamkniętym opiera się na harmonijnym współdziałaniu wielu elementów: źródła ciepła (kocioł), naczynia wzbiorczego membranowego, zaworu bezpieczeństwa, manometru, pompy obiegowej oraz armatury regulacyjnej i zabezpieczającej. Zaniedbanie któregoś z nich może prowadzić do awarii lub nieprawidłowego działania całego systemu.
Znajomość specyfiki każdego z tych elementów i ich poprawnego połączenia jest kluczowa dla projektanta i instalatora, ale również dla świadomego użytkownika, który dzięki temu może lepiej zrozumieć działanie swojej instalacji i zadbać o jej prawidłową eksploatację. Wiedza o tym, co powinno się znaleźć w typowym schemacie instalacji CO w układzie zamkniętym, pozwala również na lepszą komunikację z fachowcami i weryfikację jakości wykonywanych prac.
Przykład z życia: Częstym błędem w starszych modernizowanych instalacjach było pozostawienie zbyt małego naczynia wzbiorczego po przejściu na układ zamknięty lub zignorowanie ciśnienia wstępnego w nowo zamontowanym naczyniu. Skutkowało to ciągłym "wyrzucaniem" wody przez zawór bezpieczeństwa przy nagrzewaniu się systemu. Taki scenariusz nie tylko marnuje wodę i energię, ale przede wszystkim świadczy o braku podstawowego zrozumienia, jak działa nowoczesny schemat instalacji CO w układzie zamkniętym i co jest potrzebne, aby pracował prawidłowo i bezpiecznie.
Innym przykładem jest lokalizacja naczynia wzbiorczego. Widziałem naczynia montowane pionowo z króćcem wody skierowanym do góry, podczas gdy producent zalecał montaż z króćcem skierowanym w dół, aby uniknąć gromadzenia się powietrza wewnątrz naczynia. Niby drobiazg, a wpływa na żywotność membrany i efektywność pracy naczynia. Warto więc zawsze sprawdzić instrukcję producenta i upewnić się, że wszystkie kluczowe komponenty, tworzące szkielet schematu instalacji co w układzie zamkniętym, są zamontowane poprawnie i zgodnie z zaleceniami.
Niezbędne Zabezpieczenia i Bezpieczeństwo w Układzie Zamkniętym CO
Bezpieczeństwo w każdej instalacji grzewczej powinno być priorytetem numer jeden, ale w układzie zamkniętym, z racji pracy pod ciśnieniem i braku bezpośredniego odpowietrzania do atmosfery, nabiera ono szczególnego znaczenia. Wszelkie uchybienia w tym zakresie mogą prowadzić do bardzo poważnych konsekwencji, włącznie z uszkodzeniem systemu czy, w skrajnych przypadkach, eksplozją. Dlatego też poprawny schemat instalacji CO w układzie zamkniętym musi bezwzględnie uwzględniać szereg warstw zabezpieczeń.
Najbardziej krytycznym zagrożeniem w układzie zamkniętym jest nadmierny wzrost ciśnienia lub temperatury. Układ jest szczelny, a woda rozszerza się podczas podgrzewania. Jeśli naczynie wzbiorcze jest za małe lub uszkodzone, lub jeśli kocioł nadal generuje ciepło, a obieg wody został przerwany (np. przez awarię pompy lub brak prądu), ciśnienie i temperatura mogą szybko wzrosnąć do niebezpiecznych poziomów.
Dla ochrony przed nadmiernym wzrostem ciśnienia, jak już wspomniano, niezbędny jest zawór bezpieczeństwa ciśnieniowy. Jego prawidłowe dobranie i umieszczenie w instalacji jest elementarzem. W przypadku kotłów na paliwa płynne, gazowe czy elektryczne, gdzie jest możliwość natychmiastowego przerwania dostawy energii do palnika, ryzyko szybkiego, gwałtownego wzrostu temperatury po zatrzymaniu pompy jest mniejsze. Nowoczesne kotły gazowe czy olejowe często posiadają własne systemy bezpieczeństwa (np. czujniki przegrzewu, presostaty), które w przypadku awarii zatrzymują pracę urządzenia.
Sytuacja znacząco komplikuje się w przypadku kotłów na paliwo stałe pracujących w układzie zamkniętym. Kocioł na węgiel czy drewno po wyłączeniu wentylatora czy zatrzymaniu pompy obiegowej nadal zawiera rozżarzone palenisko, które generuje ciepło przez długi czas. Jeśli to ciepło nie zostanie odebrane z wody kotłowej, jej temperatura może szybko wzrosnąć powyżej punktu wrzenia, prowadząc do wzrostu ciśnienia pary i katastrofalnych skutków.
Dlatego też kotły na paliwa stałe przeznaczone do pracy w układach zamkniętych muszą być specjalnie przystosowane i wyposażone w urządzenia służące do awaryjnego odbioru nadmiaru ciepła. Najczęstszym i najpewniejszym rozwiązaniem jest wężownica schładzająca (nazywana też wężownicą bezpieczeństwa lub wężownicą antyprzegrzewową). Jest to element zabudowany w wymienniku kotła. Gdy temperatura wody w kotle osiągnie krytyczną wartość (zazwyczaj powyżej 95°C, ale przed osiągnięciem temperatury wrzenia), uruchamia się termostatyczny zawór bezpieczeństwa, który kieruje zimną wodę z sieci wodociągowej do tej wężownicy. Woda przepływając przez wężownicę, odbiera ciepło z wody kotłowej, obniżając jej temperaturę, a następnie gorąca woda z wężownicy jest odprowadzana do kanalizacji.
Mechanizm działania wężownicy z zaworem termostatycznym jest genialnie prosty i niezawodny, ponieważ działa niezależnie od zasilania elektrycznego – uruchamia go wyłącznie temperatura wody kotłowej. Przepływ zimnej wody wodociągowej jest grawitacyjny lub z sieci, a nie zależy od pompy CO. Koszt takiego zabezpieczenia w postaci dedykowanego zaworu termostatycznego do wężownicy to wydatek rzędu 300-600 PLN, nie licząc kosztu samej wężownicy wbudowanej w kocioł.
Należy zwrócić szczególną uwagę na wymogi normatywne dotyczące wężownic schładzających dla kotłów na paliwo stałe w układach zamkniętych. Normy te określają minimalną moc chłodzenia wężownicy, co przekłada się na wymaganą minimalną średnicę przyłączy wodnych i wymagany przepływ wody wodociągowej w razie awarii. Zaniedbanie tych parametrów sprawia, że zabezpieczenie może okazać się nieskuteczne przy dużej mocy kotła i szybko rosnącej temperaturze. Typowe natężenie przepływu wody przez wężownicę schładzającą w razie awarii dla kotła o mocy np. 20 kW może wynosić 0.2-0.5 m³/h, a w przypadku mocniejszych kotłów wartości te odpowiednio rosną. Ważne jest również, aby ciśnienie wody w sieci wodociągowej było wystarczające do zapewnienia wymaganego przepływu.
Innym kluczowym elementem bezpieczeństwa, szczególnie cennym w przypadku układów z pompą obiegową, które stają w obliczu braku zasilania, jest zawór zabezpieczenia termicznego (typu np. STS, DBV). Działa on na podobnej zasadzie co zawór do wężownicy, ale jego zadaniem jest upuszczenie gorącej wody bezpośrednio z kotła, wpuszczając w jej miejsce zimną wodę z sieci, lub uruchamiając wężownicę zewnętrznego schładzania (rzadziej stosowane). Standardowy zawór termiczny zadziała, gdy temperatura wody kotłowej osiągnie ok. 95-97°C, chroniąc przed wrzeniem. Ten typ zabezpieczenia jest często stosowany, gdy kocioł nie posiada wbudowanej wężownicy, choć w nowoczesnych, certyfikowanych kotłach na paliwo stałe do układów zamkniętych wężownica jest standardem.
Dodatkowe zabezpieczenia elektryczne w układzie zamkniętym to przede wszystkim czujniki ciśnienia i temperatury, które współpracują z automatyką kotła i pompy obiegowej. Nowoczesne regulatory mogą wyłączyć kocioł (jeśli jest to możliwe, np. w gazowym czy na pellet) lub włączyć alarm, gdy parametry wyjdą poza normę.
Co zrobić w razie braku prądu, gdy instalacja pracuje w układzie wymuszonym (praktycznie zawsze w układzie zamkniętym) z kotłem na paliwo stałe bez odpowiednich zabezpieczeń (co jest niezgodne z normami!)? No cóż, jest to scenariusz jak z koszmaru instalatora. Ciepło narasta, pompa stoi, ciśnienie i temperatura rosną błyskawicznie. Jedynym ratunkiem może być zainstalowanie systemu zasilania awaryjnego (UPS) dla pompy obiegowej i ewentualnie automatyki kotła. Zasilacz UPS do pompy o mocy ok. 25-40W to koszt 400-800 PLN, a pozwala utrzymać pracę pompy przez kilka godzin w zależności od pojemności akumulatora, co zazwyczaj wystarcza do wypalenia się wsadu paliwa w kotle lub przywrócenia zasilania głównego. Pamiętajmy jednak, że UPS nie zastępuje zabezpieczeń termicznych typu wężownica czy zawór upustowy, które są niezależne od prądu!
Nie można zapomnieć o poprawnym odpowietrzeniu systemu. Powietrze w instalacji może powodować nieprawidłowe działanie grzejników, korozję i wibracje pompy. W układzie zamkniętym proces odpowietrzania jest zazwyczaj prostszy niż w otwartym. Stosuje się odpowietrzniki ręczne na grzejnikach i w najwyższych punktach instalacji oraz często odpowietrznik automatyczny umieszczony np. przy kotle lub na pionie zasilającym.
Wreszcie, kluczowe dla długotrwałego bezpieczeństwa jest utrzymanie odpowiedniej jakości czynnika grzewczego (wody). W układzie zamkniętym, dzięki minimalnemu kontaktowi z powietrzem, woda powinna być bardziej stabilna chemicznie. Jednak zaleca się stosowanie specjalnych inhibitorów korozji i osadów, aby chronić metalowe elementy instalacji. Taki inhibitor dodany do wody raz na kilka lat (zgodnie z zaleceniem producenta) to niewielki koszt (np. 50-150 PLN za opakowanie na standardową instalację) w porównaniu do kosztów wymiany skorodowanych komponentów.
Wszystkie te zabezpieczenia – od naczynia wzbiorczego, przez zawory bezpieczeństwa, wężownice schładzające, aż po zawory termiczne i układy zasilania awaryjnego – tworzą kompleksowy schemat bezpieczeństwa instalacji CO w układzie zamkniętym. Są one nie tylko wymagane przez prawo (normy PN-EN) w przypadku pewnych typów kotłów, ale przede wszystkim stanowią naszą polisę bezpieczeństwa i gwarancję spokoju ducha podczas sezonu grzewczego. Ich prawidłowy montaż i regularne przeglądy (np. coroczne sprawdzenie ciśnienia w naczyniu wzbiorczym i stanu zaworów bezpieczeństwa) są równie ważne jak sama ich obecność.
Podsumowując ten obszar, bezpieczeństwo w układzie zamkniętym nie jest opcją, lecz bezwzględnym wymogiem, a schemat instalacji CO w układzie zamkniętym z piecem na paliwo stałe wymaga dodatkowych, bezkompromisowych zabezpieczeń termicznych. Współczesna technika oferuje sprawdzone rozwiązania, ale to od wiedzy i sumienności projektanta oraz instalatora, a następnie użytkownika, zależy, czy te zabezpieczenia faktycznie spełnią swoją rolę w razie potrzeby. Wybierając firmę do wykonania instalacji, zapytajmy wprost, jakie zabezpieczenia planują zastosować i dlaczego – to podstawowy test ich kompetencji.
Układ Zamknięty a Układ Otwarty - Kluczowe Różnice Schematów
Świat centralnego ogrzewania, choć na pierwszy rzut oka może wydawać się monolitem, w praktyce dzieli się na dwa fundamentalne modele: układ otwarty i układ zamknięty. Choć cel obu jest ten sam – dostarczyć ciepło do pomieszczeń – różnice w schemacie instalacji CO obu systemów są znaczące i wpływają na ich działanie, bezpieczeństwo, koszty instalacji i eksploatacji, a nawet na żywotność komponentów.
Instalacje centralnego ogrzewania systemu otwartego, będące historycznie starszym rozwiązaniem, charakteryzują się stałym połączeniem armatury grzewczej z powietrzem atmosferycznym. Elementem, który to połączenie zapewnia, jest otwarte naczynie wzbiorcze, umieszczone w najwyższym punkcie instalacji (np. na strychu). Naczynie to ma prostą konstrukcję, zazwyczaj jest to zbiornik wykonany z blachy ocynkowanej lub tworzywa sztucznego. Działa jako bufor bezpieczeństwa i element zarządzający zmianami objętości wody. Kiedy woda się nagrzewa i rozszerza, jej nadmiar spływa do naczynia wzbiorczego. Kiedy stygnie i kurczy się, woda z naczynia grawitacyjnie wraca do systemu. Oprócz tej funkcji, naczynie zapewnia odpowietrzanie systemu, gdyż powietrze gromadzące się w wodzie może uchodzić swobodnie do atmosfery.
Schemat instalacji otwartej może pracować w systemie grawitacyjnym (gdzie obieg wody jest wymuszany jedynie przez różnicę gęstości ciepłej i zimnej wody, co wymaga odpowiednich spadków rur i większych średnic) lub wymuszonym (z zastosowaniem pompy obiegowej). Niezależnie od typu obiegu, kluczowe jest to stałe połączenie z powietrzem poprzez otwarte naczynie wzbiorcze. Ciśnienie w takiej instalacji jest praktycznie ciśnieniem atmosferycznym plus statyczne ciśnienie słupa wody do naczynia wzbiorczego. Oznacza to, że temperatura wody w instalacji jest ograniczona do 100°C (temperatura wrzenia pod ciśnieniem atmosferycznym). Jakakolwiek próba przekroczenia tej granicy skutkuje wrzeniem wody i intensywnym parowaniem, co może prowadzić do szybkiego ubytku czynnika grzewczego.
Główną wadą systemu otwartego jest ciągły kontakt wody z powietrzem. Tlen zawarty w powietrzu rozpuszcza się w wodzie i przyspiesza korozję elementów metalowych instalacji (grzejników, rur, wymiennika kotła), skracając ich żywotność. Dodatkowo, z otwartego naczynia wzbiorczego woda stale paruje, co wymaga regularnego jej uzupełniania. W ekstremalnych warunkach (np. w zimie na nieocieplonym strychu) woda w naczyniu może zamarznąć, blokując jego działanie i stwarzając niebezpieczną sytuację dla całej instalacji. Połączenie z atmosferą sprawia również, że do wody mogą dostawać się zanieczyszczenia.
Przechodząc do układu zamkniętego – jak już szczegółowo omówiono – sercem różnicy w schemacie jest zamknięte naczynie wzbiorcze membranowe. System ten jest hermetycznie szczelny i pracuje pod ciśnieniem roboczym (zwykle od 1.2 do 2.5 bara). To brak kontaktu z powietrzem jest jego fundamentalną przewagą. Ograniczenie dostępu tlenu znacząco spowalnia procesy korozyjne, przedłużając żywotność wszystkich metalowych komponentów instalacji. Ponieważ system jest szczelny, nie ma problemu z parowaniem i koniecznością częstego uzupełniania wody (poza niewielkimi stratami przy odpowietrzaniu czy drobnych wyciekach). Układ zamknięty może pracować z wodą o wyższej temperaturze (potencjalnie powyżej 100°C, jeśli komponenty są na to przystosowane i zapewniono odpowiednie zabezpieczenia termiczne, choć w typowych instalacjach CO pracuje się w zakresie 60-80°C), a co za tym idzie, jest bardziej elastyczny pod kątem wymagań różnych typów kotłów.
Elastyczność projektowa to kolejna wielka zaleta układu zamkniętego. Ponieważ system jest z natury układem ciśnieniowym z obiegiem wymuszonym (pompa jest niezbędna), nie ma konieczności zachowania specjalnych spadków rur dla obiegu grawitacyjnego. Rury mogą być prowadzone dowolnie, co jest nieocenione w nowoczesnym budownictwie i podczas renowacji. Komponenty systemu zamkniętego (zwłaszcza naczynie wzbiorcze) są zazwyczaj kompaktowe i można je łatwo zintegrować z kotłem w kotłowni, bez potrzeby wyznaczania najwyższego punktu na naczynie.
Jednym z elementów, który często pojawia się w kontekście obu układów, zwłaszcza wymuszonych i z kotłami na paliwo stałe lub wymagającymi ochrony powrotu, jest zawór czterodrogowy (lub trójdrogowy z odpowiednim sterowaniem). Choć źródło danych wspomina go w kontekście układu otwartego z obiegiem wymuszonym, zawory mieszające są powszechnie stosowane w obu typach systemów. Ich rola to mieszanie gorącej wody z zasilania kotła z chłodniejszą wodą powracającą z instalacji. W przypadku kotłów stałopalnych, zawór ten podnosi temperaturę wody wracającej do kotła (temperatura powrotu), zapobiegając kondensacji pary wodnej na zimnych ściankach wymiennika, co mogłoby prowadzić do jego szybkiej korozji i zniszczenia. W innych systemach (np. z grzejnikami i ogrzewaniem podłogowym) zawór może być używany do obniżenia temperatury wody kierowanej do pętli podłogowych (np. do 35-45°C), podczas gdy do grzejników może płynąć woda o wyższej temperaturze.
Powiedziałbym, że w typowej nowoczesnej instalacji mieszkaniowej, podstawowy schemat instalacji CO oparty o układ zamknięty jest domyślnym wyborem ze względu na bezpieczeństwo, komfort eksploatacji i żywotność. Wyjątki? Czasem w bardzo specyficznych, starszych instalacjach z kotłami, które nie spełniają rygorystycznych norm bezpieczeństwa dla układów zamkniętych, pozostaje się przy układzie otwartym. Dane mówią też o sytuacji, gdy zasilanie wodociągowe jest niepewne (hydrofor z możliwością zaniku ciśnienia) lub występują częste i długotrwałe przerwy w dostawie prądu, a zastosowanie kotła na paliwo stałe bez absolutnie pewnych, niezależnych od prądu zabezpieczeń termicznych jest problematyczne. W takich skrajnych scenariuszach, pomimo wszystkich jego wad, układ otwarty bywa jeszcze rozważany, głównie ze względu na prostotę i mniejsze zależności od zewnętrznych dostaw.
Jednak rynek i regulacje skłaniają ku rozwiązaniom zamkniętym. Współczesne kotły na paliwa stałe, które mają pracować w domowych instalacjach grzewczych, są już projektowane z myślą o pracy w układzie zamkniętym i posiadają wbudowane, certyfikowane zabezpieczenia termiczne (jak wężownica schładzająca), co minimalizuje ryzyko związane z brakiem prądu czy innymi awariami obiegu. Koszt inwestycji w nowoczesny kocioł i system zamknięty często zwraca się w dłuższej perspektywie poprzez niższe koszty eksploatacji (brak korozji, brak uzupełniania wody) i wyższe bezpieczeństwo.
Podsumowując różnice schematów: układ otwarty to rozwiązanie starsze, prostsze konstrukcyjnie (poza wymaganiami grawitacji), ale obarczone ryzykiem korozji, parowania, zamarzania naczynia i ograniczoną temperaturą pracy. Typowy schemat instalacji co w układzie otwartym cechuje obecność dużego naczynia w najwyższym punkcie i luźniejsze podejście do szczelności. Układ zamknięty to system nowoczesny, pracujący pod ciśnieniem, wymagający dokładnego montażu i specyficznych zabezpieczeń, ale oferujący dłuższą żywotność, wyższe bezpieczeństwo, brak strat wody przez parowanie i dużą swobodę projektową rurociągów. Schemat instalacji CO w układzie zamkniętym poznajemy po charakterystycznym czerwonym lub niebieskim (dla CWU) membranowym naczyniu ciśnieniowym w kotłowni.
Można powiedzieć, że ewolucja od układu otwartego do zamkniętego to krok od systemu "samoregulującego się" (w ograniczonym stopniu, poprzez przelew) do systemu precyzyjnie kontrolowanego i zabezpieczonego. Decyzja o wyborze systemu powinna być podyktowana typem kotła, dostępnością mediów (prąd, woda wodociągowa pod ciśnieniem), warunkami panującymi w miejscu instalacji oraz przepisami, które jasno określają, kiedy dany typ układu może być stosowany.
Nawet tak podstawowe elementy jak zawory odcinające różnią się często jakością i specyfikacją w systemach otwartych i zamkniętych. W układzie zamkniętym, gdzie ciśnienie jest wyższe, wymagane są zawory o odpowiednich parametrach ciśnieniowych. Różnice te, choć pozornie drobne, składają się na całościowy schemat wykonania instalacji co w układzie zamkniętym i odróżniają go od rozwiązania otwartego, czyniąc go zazwyczaj bardziej zaawansowanym technicznie i bezpiecznym, o ile jest prawidłowo wykonany.
Z moich doświadczeń wynika, że głównym powodem problemów w układach zamkniętych jest albo zaniedbanie podstawowych zabezpieczeń (np. brakujący lub źle dobrany zawór bezpieczeństwa), albo nieprawidłowe działanie lub dobór naczynia wzbiorczego. Kiedy te kluczowe elementy schematu instalacji co w układzie zamkniętym są poprawne, system działa latami bezawaryjnie. Kiedy są pominięte lub wadliwe, mogą prowadzić do sytuacji kryzysowych. Dlatego kluczowe jest, aby każdy element był na swoim miejscu i spełniał swoją funkcję, a całość instalacji była zaprojektowana i wykonana przez osoby z odpowiednią wiedzą i doświadczeniem w pracy z systemami ciśnieniowymi.